石墨加工中心的动态切削过程优化
石墨加工中心与动态切削技术简介
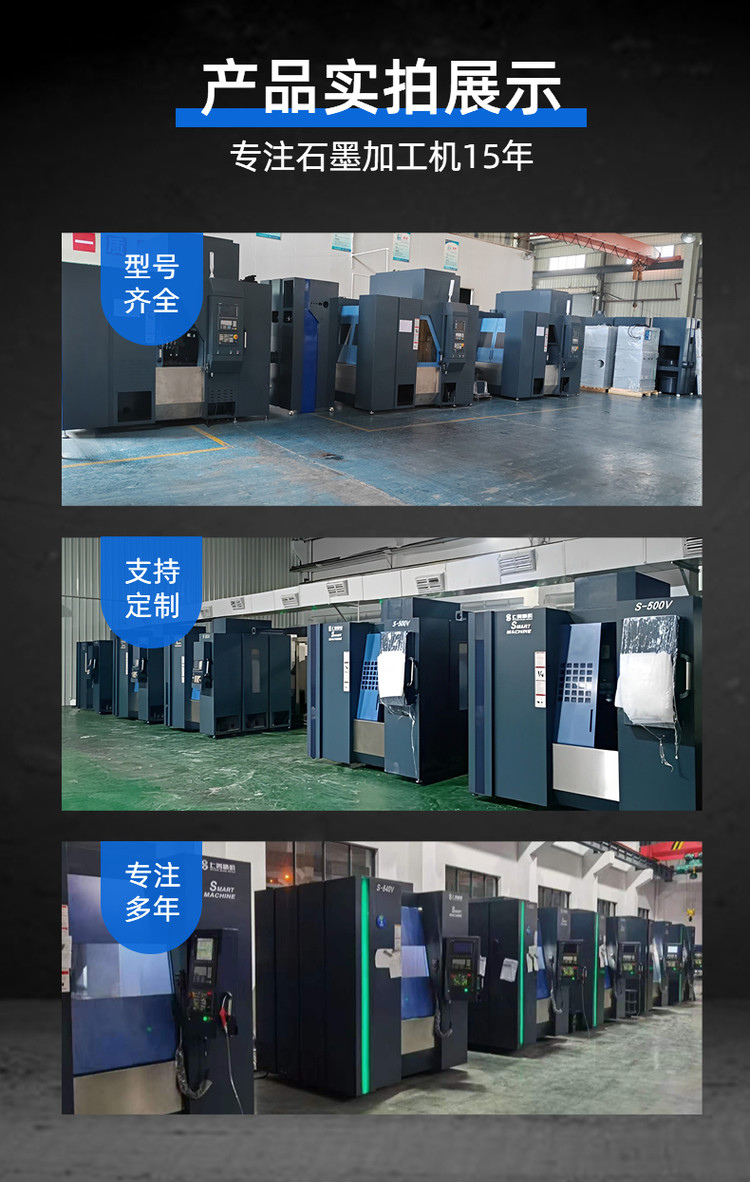
石墨加工中心是一种专用于石墨加工的高精度机床。它在切削加工石墨材料时,采用的是动态切削技术,通过刀具高速旋转和进给运动实现工件的加工。动态切削过程的优化,可以提高加工效率和精度,降低刀具损耗和加工质量变差的风险。
此文章由AI生成,如有侵权或错误请联系修改,谢谢!动态切削过程的优化方法
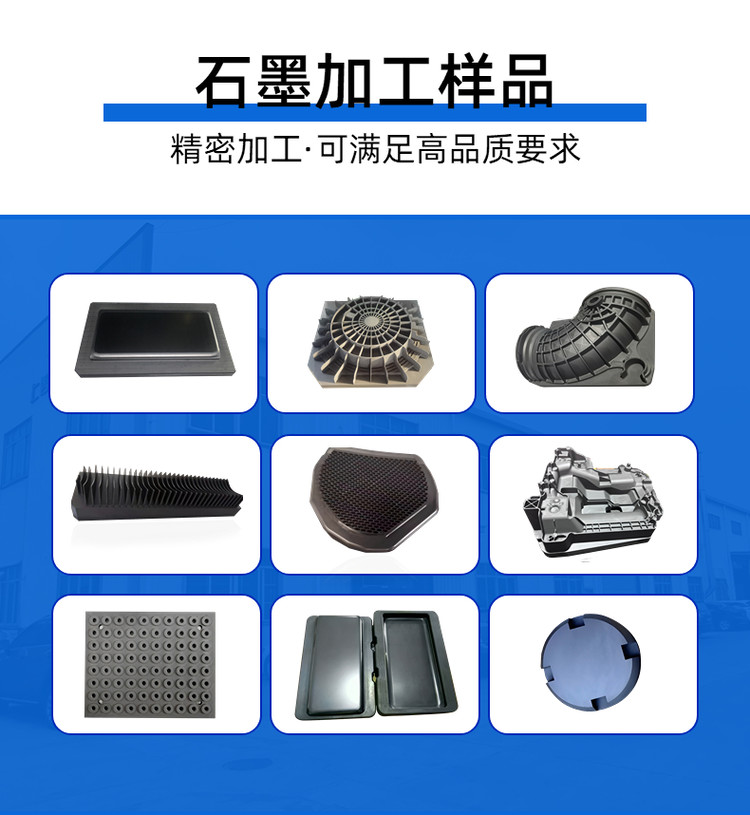
1. 切削速度的选择
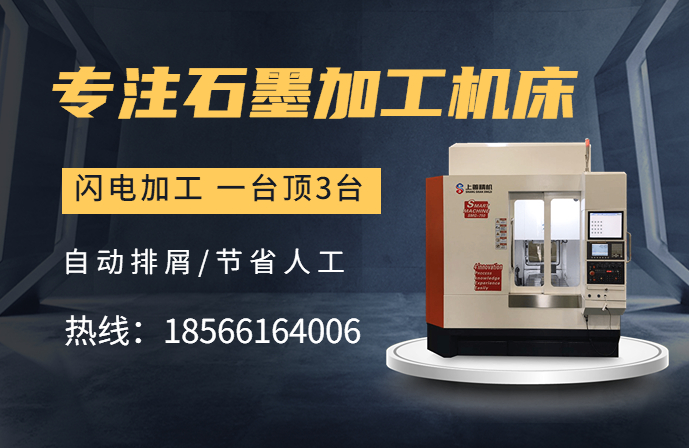
切削速度是指刀具切削石墨材料时的线速度。选择适合的切削速度可以提高加工效率和加工质量,同时减少刀具磨损。切削速度的选择需要考虑刀具材料、刀具直径和加工深度等因素。
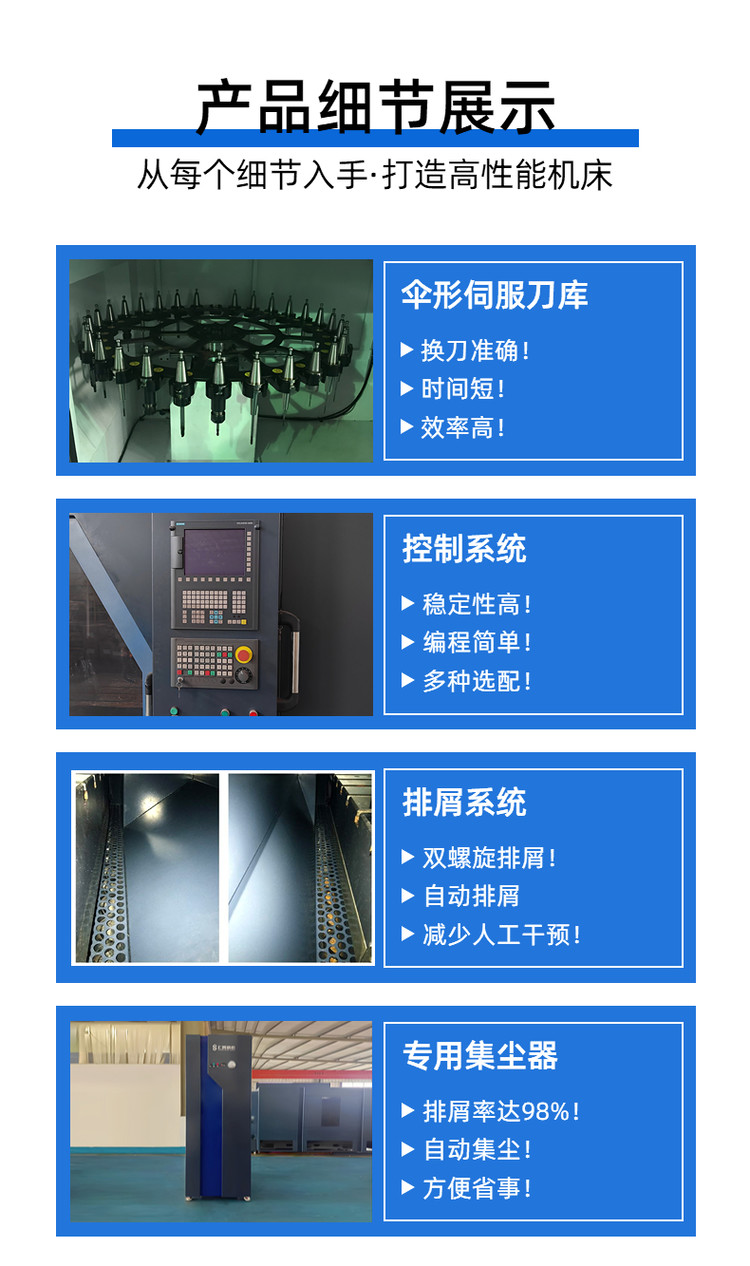
2. 进给速度的控制
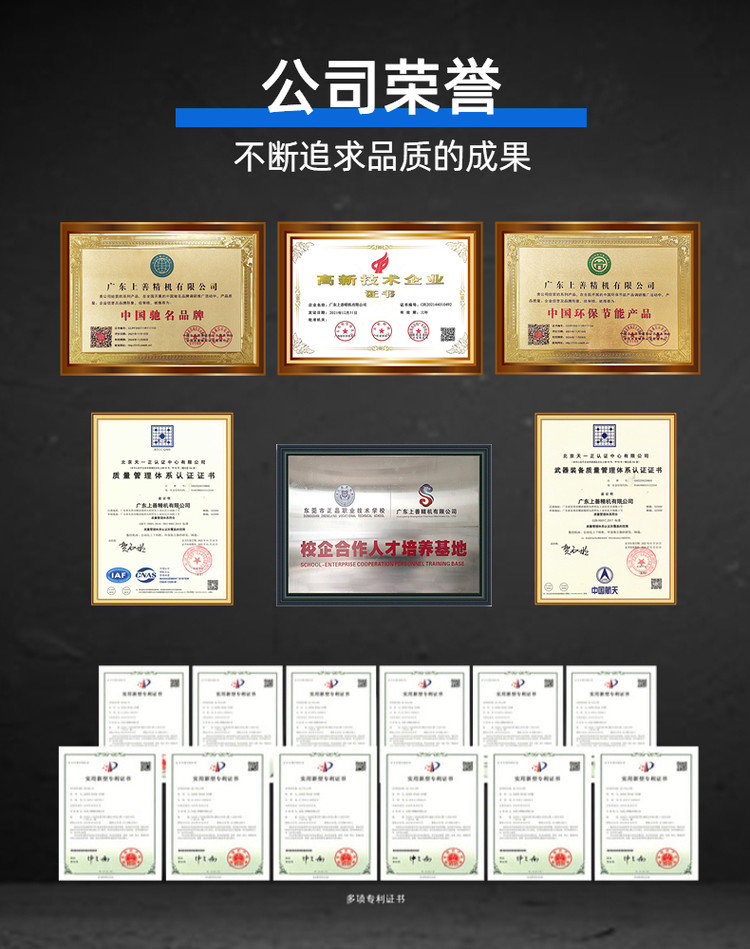
进给速度是指切削过程中工件的移动速度。合理控制进给速度可以保证刀具和工件之间的接触时间合适,避免过快或过慢造成的加工质量问题。进给速度的选择需要根据工件材料和加工要求来确定。
3. 切削深度的调整
切削深度是指刀具在一次切削过程中,与石墨材料接触的距离。适当调整切削深度可以平衡加工效率和加工质量。切削深度需要根据刀具和工件的结构情况来确定,同时要考虑刀具的刚性和加工表面的要求。
4. 切削方式的选择
石墨加工中心常用的切削方式包括铣削、镗削和钻削等。不同的切削方式适用于不同的加工情况,选择合适的切削方式可以提高加工效率和加工质量。切削方式的选择需要综合考虑工件材料、尺寸和形状等因素。
5. 刀具的优化设计
刀具是动态切削过程中的关键部件。优化刀具的设计可以提高切削稳定性和加工质量。刀具的优化设计需要考虑材料选择、刃状结构和刀具几何形状等因素,以满足石墨加工的特殊需求。
动态切削过程优化的效果
通过对石墨加工中心动态切削过程的优化,可以实现以下效果:
1. 提高加工效率和精度。
优化切削参数和刀具设计,可以减少加工时间,提高加工效率。同时,精确控制切削过程中的参数和环境变量,可以提高加工精度。
2. 降低刀具损耗。
通过优化切削参数和刀具设计,可以减少刀具磨损,延长刀具寿命。同时,合理选择切削方式和切削深度,可以降低刀具的切削负荷。
3. 减小加工表面的残余应力。
优化切削方式和刀具设计,可以减小切削过程中产生的热影响区域,降低加工表面的残余应力,提高加工质量。
4. 提高加工质量的稳定性。
通过优化切削参数和刀具设计,可以提高切削过程的稳定性,减少加工质量的波动。同时,合理控制切削速度和进给速度等参数,可以减少加工过程中的振动和共振。
总之,动态切削过程的优化是石墨加工中心技术发展的重要方向。通过合理选择切削参数、切削方式和刀具设计,可以提高加工效率和加工质量,降低刀具损耗和加工风险,满足石墨加工的特殊需求。