加工过程中如何优化钨钢材料的切削性能?
掌握切削参数选择
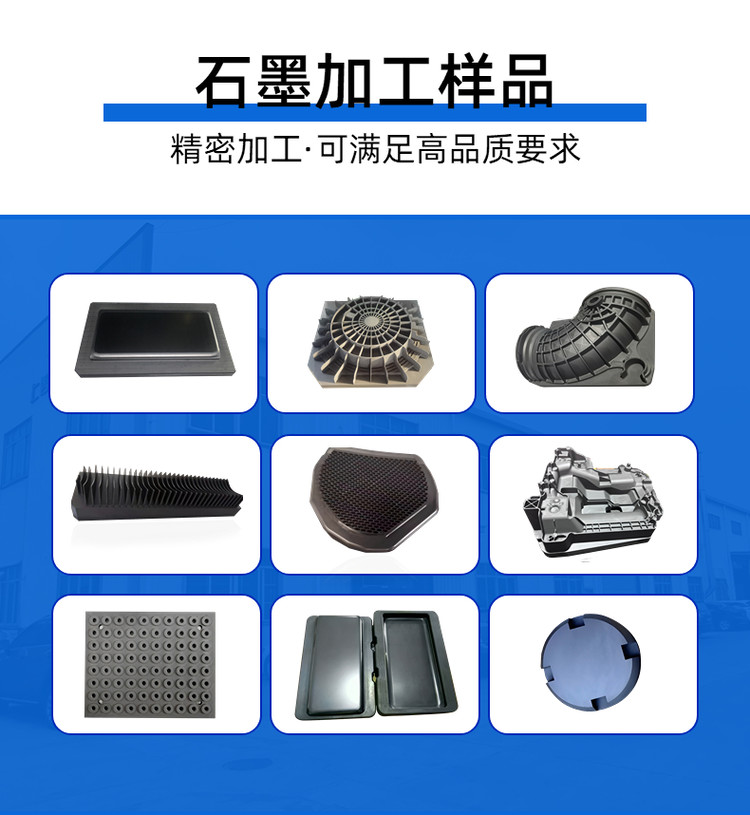
切削参数的选择是优化钨钢材料切削性能的关键。对于钨钢材料来说,合理的切削速度、进给率和切削深度可以有效提高切削效率和降低切削负荷。根据钨钢材料的硬度和切削实验,可以通过试验和经验确定合适的切削参数,以获得最佳的切削性能。
此文章由AI生成,如有侵权或错误请联系修改,谢谢!选择合适的切削刀具
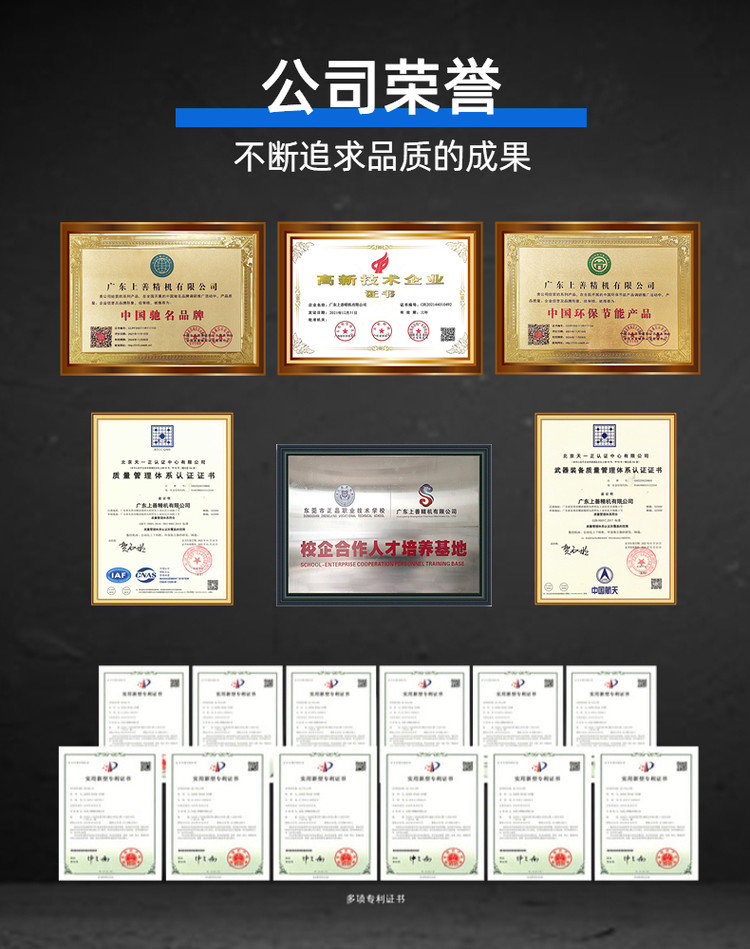
切削刀具的选择对钨钢材料的切削性能有很大的影响。首先,要选择硬度高、耐磨性好的切削刀具,以保证切削刃的锋利度和切削面的光洁度。其次,根据加工要求和切削形式,选择合适的切削刀具类型,如铣刀、车刀或钻头,以最大限度地提高切削效率和工件表面质量。
优化切削润滑方式
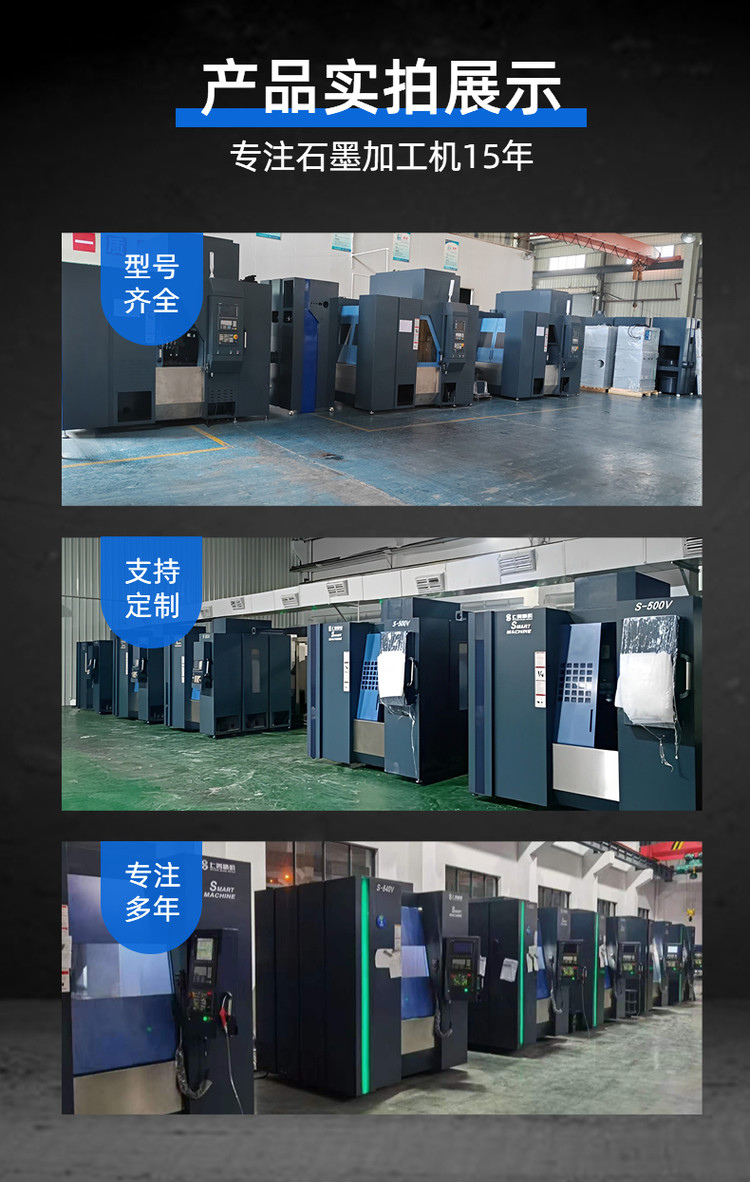
切削润滑是优化钨钢材料切削性能的重要因素之一。通过选择合适的切削润滑方式,可以减少切削时材料与刀具的摩擦,降低切削温度,延长刀具寿命,同时改善加工表面质量。常用的切削润滑方式包括干切、切削液冷却和轮道润滑等,需要根据具体情况选择合适的切削润滑方式。
合理选择切削策略
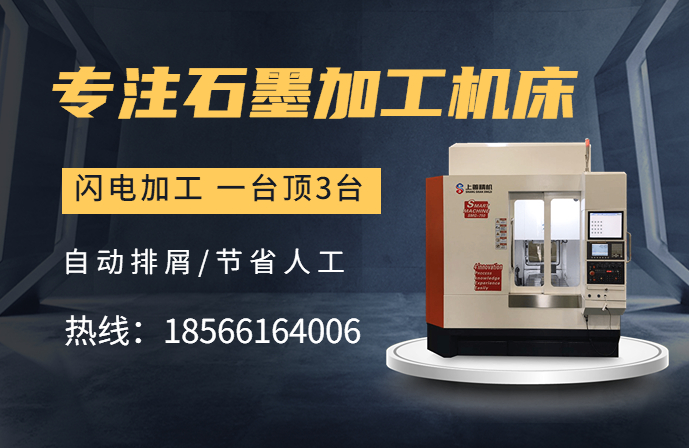
合理的切削策略也对钨钢材料的切削性能优化起到重要作用。例如,对于复杂的切削轮廓,可以采用多道切削或分段切削的方式,以减轻切削负荷和提高切削效率。另外,选择合适的切削路径和切削方向,有利于减少切削振动和切削力,提高切削表面精度和加工精度。
定期保养和更换切削工具
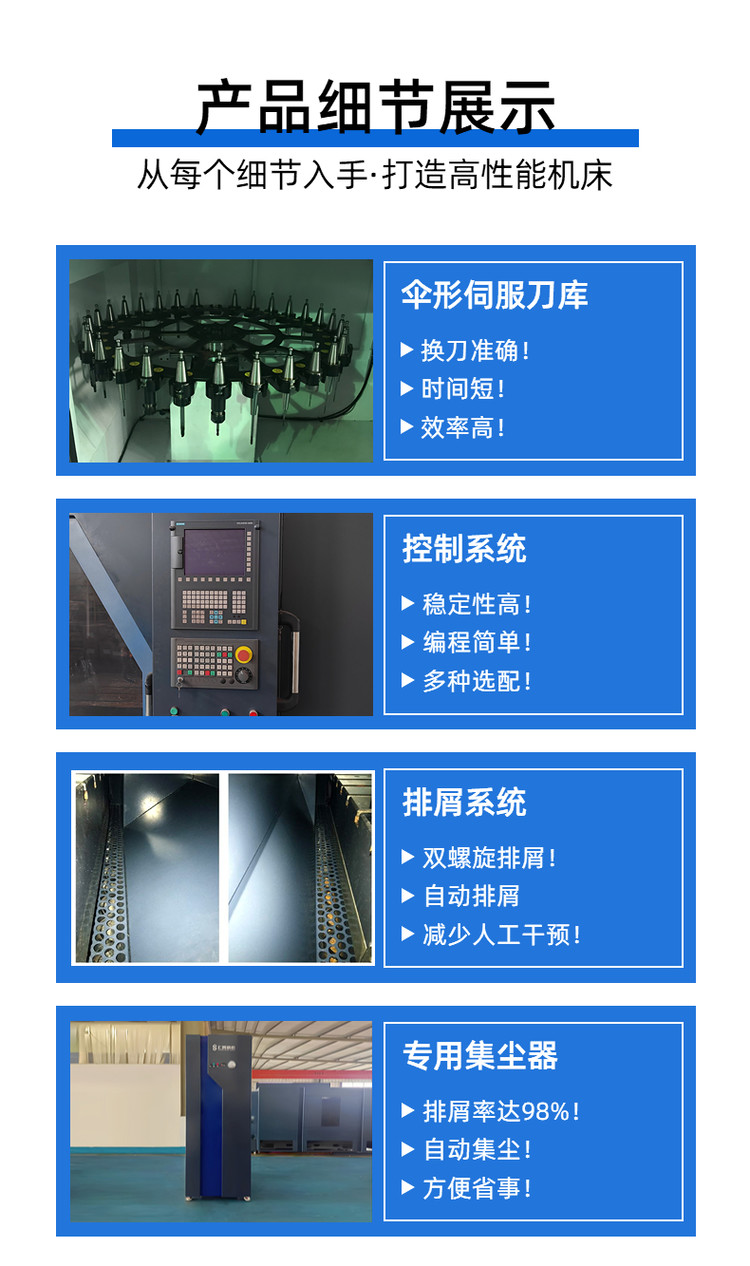
定期保养和更换切削工具是优化钨钢材料切削性能的重要环节。切削工具的正常磨损会导致切削边界磨损、切削力增加和切削表面质量下降等问题。因此,定期对切削工具进行磨削和涂覆等维护工作,可以提高切削工具的耐磨性和使用寿命。同时,根据切削工具的磨损情况,及时更换刀具也是保证切削性能的一种重要方式。
通过合理选择切削参数、优化切削刀具、切削润滑、切削策略和切削工具的保养和更换,可以有效提高钨钢材料的切削性能。在实际应用中,还需根据具体加工要求和条件进行综合考虑和优化,以获得最佳的切削效果。